Meet Dr. Ing. Paul Refalo from the Faculty of Engineering at the University of Malta
Meet Dr. Ing. Paul Refalo, Senior Lecturer at the Faculty of Engineering at the University of Malta. We are honoured to introduce Dr. Ing. Paul Refalo to the Green Deal Malta platform! In our exclusive interview with Dr. Refalo, he explains some of the main initiatives which the Department of Industrial and Manufacturing Engineering at the University of Malta is currently working on in terms of the green transition, and gives an overview of some of the studies which have been published in peer-reviewed journals and conferences. He also explains how, in his opinion, researchers and academics can participate or contribute to making Malta more sustainable and he explains how sustainability is not just ‘achieved’ by having a PV system on a roof, yet it is about addressing the environmental, financial, and social pillars from systems and life-cycle perspectives. Dr. Refalo also speaks about certain shifts in consumer trends that are being experienced in the engineering industry, towards products that are labelled as eco and environmentally friendly. Have a look at our interview with Dr. Refalo to find out more!
What are the main initiatives which the Department of Industrial and Manufacturing Engineering at the University of Malta is working on in terms of the green transition?
My main area of research towards sustainable manufacturing focuses on Resource Efficiency in processes and products. The manufacturing industry uses various resources such as raw materials, energy, water and compressed air. We have various research projects at different levels targeting the efficiency of these different resources. Our main goal is to identify the parameters which affect resource consumption the most and assess different approaches which reduce the environmental footprint of manufactured products.
Some of the studies which have been published in peer-reviewed journals and conferences are briefly explained below.
Compressed Air
Pneumatic powered components provide a safe and reliable opportunity to automate production lines in the manufacturing industry. Compressed air systems are notoriously expensive to operate as a result of system losses and inefficiencies. Typical systems have an output efficiency of 10-15%. This offers a significant improvement opportunity to meet sustainable targets concerning energy consumption in industry and lower life cycle energy impacts. Amongst various inefficiencies, leakages and excessive pressures are identified as some of the most common sources of waste. The scope of this research study was to assess the sustainability impact of various compressed air shortcomings. Simulations were carried out under experimental conditions to measure the additional energy consumption and compressed air volume required for different pneumatic scenarios. The results showed that repairing one leak of 1.5mm in diameter in a system operating at 6 bar could potentially save around 4,000 kWh of electrical energy per year. This amounts to €470 of additional electrical costs and 1.8 tonnes of carbon dioxide emissions per leak. Such waste could easily offset the benefits gained from the implementation of renewable energy sources. Just for simple comparison purposes, it was shown that such a small leak would offset the same amount of electricity generated by ten photovoltaic panels installed in Malta per year. A large compressed air system could easily include several unnoticed leakages along its distribution network which would ultimately have a direct effect on both the life cycle of the production systems as well as the products produced.
Plastic Injection Moulding
Sustainable manufacturing has become essential amongst industries of all types due to the diminishing non-renewable sources and an ever-increasing demand for environmentally friendly products. Injection moulding is one of the most widely used processes for the production of plastic products and is a large consumer of energy. Energy efficiency has become a serious concern due to the rising energy costs and the associated environmental impacts. It is estimated that one third of the global energy consumption and 36% of CO2 emissions are attributed to the manufacturing sector. The aim of this study was to optimize the injection moulding process in order to reduce energy consumption whilst also ensuring no loss in part quality. This was achieved by investigating the impacts of cooling time, screw rotational speed, mould temperature and nozzle temperature. It was found that the cooling time and the nozzle temperature had the greatest impact on energy consumption. Results indicated a possibility of using lower cycle times and lower nozzle temperatures to decrease energy consumption without having adverse impacts on part quality. When comparing the energy consumption while using process parameters set at their minimum values compared to typically set values, savings of 14% were achieved.
Raw Materials and Recycling
Another study focused on a conventional recycling system currently implemented in a local polymer manufacturing facility and assessed potential alternative approaches that can sustainably improve upon it. This was done by analysing different ratios of virgin to recycled plastics, one of which consisted of 100% recycled material, and by examining the reprocessing capability of the materials involved. Factors affected by these changes were studied, including product quality, material, energy and water consumption, maintenance, and also human labour. The effects of such variables were then analysed in terms of appropriate sustainability indicators, relating to the three pillars of sustainability: economy, environment and society. Through this sustainability analysis, it was shown how a cascade recycling system can be applied, in which manufacturing starts with just virgin resin and cascades to the following generations of recycled material without blending with virgin resin along the process. This was proved viable up to the three reprocessing cycles. Furthermore, this study concluded that when compared to a scenario where no recycling is carried out, the implementation of such a system would reduce the carbon footprint by 29% and the costs by 28%. When compared to a typical in-house recycling system (which blends virgin and recycled materials), cascade recycling would further reduce the costs by 12% and the carbon footprint by 13%.
Life Cycle Assessment
The cosmetic industry contributes significantly to the global plastic consumption. By conducting a Life Cycle Assessment, the primary goal of this study was to analyse the life cycle environmental impacts of reusable and recyclable cosmetic packages. Different versions were assessed, applying different rates of dematerialisation, adding recycling and reuse potential, and altering the package’s design to study the effect that this has on sustainability. The environmental footprint with regards to all phases of the plastic package’s life cycle, i.e. raw material extraction, manufacturing, transportation, use, and end of life, was analysed. It was found that the raw material extraction and manufacturing stages were the most environmentally harmful stages. Results showed that manufacturing in Malta proved to be 13% more environmentally friendly than manufacturing in China. Findings also showed that eliminating the use of an aluminium component within the particular cosmetic package assessed would reduce the environmental impacts by 74%. The most environmental conscious version resulted in being the version which is both reusable and recyclable. However, both package reuse and recycling at the end-of-life hinge on the user’s aptitude and the waste management infrastructure of the brand and/or the country.
In your opinion, how can researchers and academics participate or contribute to making Malta more sustainable? What impacts does the University of Malta have on the evolution of the manufacturing industry in this regard?
It is of utmost importance that professionals working in the manufacturing industry are aware of how their operations affect sustainability at large. It is also equally important that they are aware how they can contribute towards the United Nation’s Sustainable Development Goals (SDG) today, not only in the future. SDG 12 focuses specifically on Responsible Consumption and Production and its main goal is to increase resource efficiency and to decouple economic growth from environmental degradation.
Sustainability is not just ‘achieved’ by having a PV system on a roof. Sustainability is about addressing the environmental, financial and social pillars from systems and life-cycle perspectives.
There is no one-size-fits-all solution to the problem, especially when you compare different factories processing different raw materials, producing a variety of products. The manufacturing industry is also experiencing its fourth industrial revolution which builds on the digital transformation and uses smart technology such as industrial internet of things, artificial intelligence, and machine learning. Hence more research needs to be carried out in order to propose solutions which are assessed from a total life cycle point of view, and which are both smart and sustainable.
This is what we’re doing at the Department of Industrial and Manufacturing Engineering at the University of Malta. We first train our students, Malta’s future engineers at both undergraduate and postgraduate levels. Then we carry out research on various topics, some of which are highlighted in this interview. Our research addresses real industrial problems, many of which would be provided to us by our partners in industry. We also participate in funded research projects where we collaborate directly with industrial partners and come up with solutions, new or modified processes, equipment or products which would eventually reduce the environmental and financial impacts of the manufacturing industry.
How are students involved in the green transition? Are there any specific units or courses available at the Faculty of Engineering in this regard?
Our department offers specific study-units within the Programme of Studies in Mechanical Engineering which cover Sustainable Engineering, Sustainable Manufacturing, and Sustainable Product Development. These study units, which form part of undergraduate (B.Eng. Hons) and postgraduate (M.Sc.) taught courses, cover the fundamentals required to design and assess the sustainability impacts of products and their manufacturing processes. Students, and hence our future graduates, are well equipped with the basic skills required to apply sustainability thinking in industry.
We also offer postgraduate opportunities by Research where students choose to pursue their studies at Master (by research) or PhD levels, and work towards solving a specific research problem or answer a particular research question. Students can either carry out research on the sustainability of a product (or family of products), or else on the materials and processes required to produce such products. When we participate in funded research projects, we also offer remunerated opportunities and/or scholarships whereby we engage Research Support Officers to work as part of the project research team.
Are you seeing any trends or a conscious shift in the engineering industry which promote more sustainable practices in projects or products?
It is now more evident than ever that global warming and climate change are real. Such issues shouldn’t be recognised as concerns of the future generations but should be on our top priority agenda, now and today. Companies and manufacturing firms are becoming increasingly aware of current environmental issues and that they must act now and urgently. However, both the global population and affluence are on the increase and unfortunately the current mitigating efforts are just not enough to have a net positive impact.
Various regulations and targets are helping companies align their goals towards sustainability. Energy efficiency, renewable energy, waste management, raw material substitutes, biobased and biodegradable materials, circular economy, recycling, water saving and reuse, are just some of the issues which are being targeted and acted upon. Directives, Regulations, Goals, and Strategies all help towards sustainable development.
However, we are also seeing a consumer shift towards products which are labelled as eco and environmentally friendly. It is this shift, which should be further accelerated by governmental initiative and incentives, which would eventually make the real difference.
In order to maintain their competitive advantage, companies would then find it simpler to strive towards sustainability. It is our responsibility as researchers and academics, to provide the local and global industry and governments with well-thought and life-cycle assessed solutions, processes and products which are not only technically viable and environmentally benign, but which are also financially feasible in the long-term. It is only then that a product or process can be coined as sustainable.
Contributor(s)
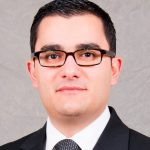
Dr. Ing. Paul Refalo
Dr Ing. Paul Refalo graduated in Mechanical Engineering from the University of Malta in 2007. After working for a building services consultancy firm, in 2009 he was appointed Research Engineer at the University of Malta on a project financed by the Malta Council for Science and Technology. He obtained his PhD in Mechanical Engineering with a thesis on Solar Desalination of Seawater in 2015. Dr Refalo joined the Department of Industrial and Manufacturing Engineering as an academic in 2012 and is currently a Senior Lecturer. His main research interests include sustainable manufacturing, resource efficiency in industry, and sustainable water treatment. He has published and presented several papers in international journals and conferences related to the sustainability of compressed air consumption and injection moulding, energy and resource efficiency in manufacturing and sustainable water treatment. He is registered with the Regulator for Energy and Water Services (REWS) as an Energy Auditor and as an Energy Performance of Buildings (EPB) Assessor. He was appointed consulting engineer on various industrial and research projects related to energy management, renewable energy technologies and sustainability in buildings.